硅微粉具有优良的物理和化学性能,可广泛应用于橡胶、塑料、高级油漆、涂料、耐火材料、电器绝缘、电子封装、高档陶瓷、精密铸造等生产领域。许多应用领域对超细硅微粉的纯度、粒度和粒度组成有相当严格的要求。硅微粉生产工艺一般有破碎、粉磨工序。粉
磨一般用滚动球磨、搅拌球磨、振动球磨、气流磨等。搅拌磨与其它超细粉碎设备相比,具有粉碎效率高、能耗低、产品粒度细、污染小、工艺过程简单等优点 。
本文采用钇稳定氧化锆珠为研磨介质,将研磨桶内壁和搅拌器都衬以聚氨酯,通过搅拌磨制备高纯超细硅微粉,对硅微粉特征参数D 。随搅拌粉磨时间延长的变化规律、钇稳定氧化锆珠对硅微粉的污染程度、1m以下超细硅微粉的形貌特征等展开研究。
1 实验条件及方法
1.1 主要原材料和仪器
石英粉:以脉石英为原料经过选矿提纯后的石英粉,其SiO 的含量为99.94% ,一0.074 mm粒级占37.39% ;钇稳定氧化锆珠:材质密度为6.0 g/cm ,莫氏硬度9,直径为3 mm;湿磨分散介质:蒸馏水。
ZJM20T搅拌球磨机(内壁及搅拌器均衬上聚氨酯),球磨桶容积为6 L,搅拌器可调转速范围:0~1 200 r/rain,人料粒度尺寸小于0.25 mm;LS—POP型激光粒度分析仪;纳米粒度与Zeta电位分析仪:型号为Zetasizer Nano ZS90;JSM一6380LV型扫描电子显
微镜。
1.2 实验方法
根据搅拌球磨机的使用说明,计算确定介质球装填量、物料装填量和湿磨分散介质体积。经计算得,料:水:研磨体质量比为1.57 kg:2.11 kg:10.26 kg,即1:1.34:6.54。通常情况下,料:水:研磨体质量比为1:(0.8~1.1):(1.5~2.3)是适宜范围¨j,但亦可根据具体情况调整比例。由于受材料的尺寸大小和密度的影响,实际选用这个比例是合适的。实际装料时介质球与浆料的总体积为球磨桶体积的75% ~80%。搅拌球磨机的转速定为600 r/min。用欧美克激光粒度分析仪测定粉磨不同时间后的硅微粉的粒度分布,用纳米粒度与Zeta电位分析仪测定***终硅微粉的粒度分布,用扫描电子显微镜观察分析硅微粉的形貌特征。
2 实验结果与讨论
目前相关行业对高纯超细硅微粉的质量要求如下:纯度即SiO 含量99.5% ~99.9% ;杂质要求:Fe 0 含量0.008% ~0.03% ,A120 含量0.06% ~0.2% ,MgO含量0.002% ,Na20含量0.O1% ,TiO2含量0.01% ;灼烧失量0.1% ~0.15% ;中位径D50( m):2.5~150,7~35,8~25,33~150。
2.1 粉磨时间对硅微粉粒度的影响
粉磨不同时间后硅微粉粒度分布和变化分别见表1~表8。
由表1可知,粉磨6 h后硅微粉的中位径,) 。是32.50 m。由表2可看出,粉磨6 h后硅微粉的粒径是43.9 m时的微分分布***,是7.17% ;***粒径是169.0 m,对应的微分分布为1.07%。
从表3可以看出,粉磨8 h后硅微粉的中位径D 。
是30.54 ixm。由表4可以看出,粉磨8 h后硅微粉的粒径为43.9 m时微分分布***,为6.58% ;***粒径169.0 m,对应的微分分布为1.32%。
由表5可知,粉磨10 h后硅微粉的中位径D 。是14.23/a,m。由表6可以看出,硅微粉的粒径为22。4Ixm时的微分分布***,为5.75% ;***粒径169.0m,其对应的微分分布为0.18%。
由表7可以看出,粉磨12 h后硅微粉的中位径D 是5.24 Ixm。由表8看出,硅微粉的粒径为8.14 m时的微分分布***,为6.48% ;***粒径72.8 I.Lm,其对应的微分分布为0.01%。不经分级可以获得百分含量占99.99% 、粒径为61.5 Ixm以下的硅微粉。
研究粉磨不同时间后硅微粉粒径特征参数的变化规律,可以近似地了解搅拌磨粉磨石英粉的难易程度或粉磨动力学。以粉磨不同时间后的硅微粉粒径特征参数D 为纵坐标,粉磨时间为横坐标作图,可得粉磨不同时间后粒径特征参数的变化规律曲线,见图1。
由图1可以看出,当粉磨时间由6 h到8 h,石英粉的特征粒径变化较小,这可能是由于石英砂粒度较粗时,磨介的冲击力相对较小,不足以粉碎石英颗粒。当粉磨时间由8 h延续至12 h,D 。变小的速度明显增大,说明磨介的粉碎力适合于磨细试验时的石英砂粒度。
2.2 ***终硅微粉粒度分析
由表8可以得知,在粉磨12 h后,物料粒度在1m左右以下的仅占11.65% ,故要通过沉降分级才能获取1 I.Lm以下的石英粉体。若要增加1 txm以下的石英粉体产量,还需继续延长搅拌研磨时问。将粉磨12 h后的石英粉在1 000 mL的量筒中进行自由沉降分级,沉降时间为14 h,之后设法收集量筒中悬浮液中的硅微粉,将此硅微粉用纳米粒度与Zeta电位分析仪测定其粒度,粒度微分分布示于图2。从图2可以看出,用搅拌磨粉磨后再经分级可以制得小于1 Ixm的石英粉,可满足高科技行业对原料粒度的要求。仪器分析测得粉末的平均粒径为624.7 nm。
2.3 硅微粉的扫描电子显微镜分析
将***终所得硅微粉在扫描电子显微镜下进行形貌观察,照片见图3。由图3可以看出,绝大部分硅微粉的粒径在1 m以下,且多数颗粒粒度均匀、形貌呈不规则的角砾状,仅有少数颗粒呈针状,但是呈球形的颗粒很少。这主要是因为粉磨介质球和物料在搅拌器的驱动下作无规则的多维循环运动和自转运动,物料在介质球的冲击力、剪切力、研磨力等多种作用力下,不断被粉碎所致。加之石英晶粒力学性能上的多向异性,也可能导致这种现象的发生。
2.4 ***终所得硅微粉的化学成分及被污染的程度
***终硅微粉的化学成分见表9。由表9可知,***终硅微粉的SiO,含量可达到99.9l% ,其它组分含量很低,已达到和超过环氧塑封料等用途的硅微粉品质要求。***终硅微粉被污染的程度小,由于研磨介质球磨损带进的ZrO 杂质仅占0.0246% ,带进的Y O 杂质为0.0014%
3 结 论
1)用搅拌磨在适当转速、适当磨矿浓度和合适的磨介充填量情况下,经过12 h的粉磨,可获得粒径为1 I.tm以下含量占11.65%的硅微粉;通过沉降分级可以获取SiO,的含量为99.91% 、1 txm以下的硅微粉。不经分级可以获得粒径为61.5 laxn以下占99.99% 的硅微粉。
2)用内衬聚氨酯的搅拌磨,以密度为6.0 g/cm 、直径为3 mm的钇稳定氧化锆珠为研磨介质,可将高纯石英砂原料磨细成SiO 的含量为99.91% 的硅微粉,从化学成份和粒度考虑,可达到一般高纯超细硅微粉的质量要求,甚至可达到和超过一般环氧塑封料用硅微粉的品质要求。
3)用搅拌磨制备的石英微粉,多数颗粒粒径均匀,但即使粒径小于1 m,仍有少数颗粒呈石英晶形的长条状,难以获得球形硅微粉。
4)***终硅微粉被污染的程度小,由研磨介质磨损带进的ZrO 杂质仅占0.0246% ,带进的Y。O。杂质为0.0014% 。
610

- 1无卤低烟阻燃材料中炭黑含量检测结果异常情况的分析
- 2GB 36246-2018中小学合成材料面层运动场地全文
- 3ASTM-D638-2003--中文版-塑料拉伸性能测定方法
- 4GBT 15065-2009 电线电缆用黑色聚乙烯塑料
- 5GB_T2951.41-2008电缆和光缆绝缘和护套材料通用试验方法
- 6GBT 13021-2023 聚烯烃管材和管件 炭黑含量的测定 煅烧和热解法
- 7PEG熔融相变温度测试
- 8聚碳酸酯(PC) DSC测试玻璃化转变温度
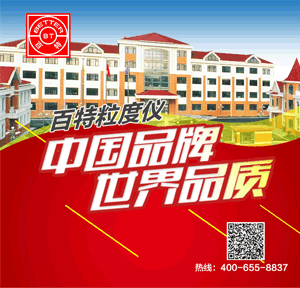
- EVA型热熔胶书刊装订强度检测与质量控制研究
- 自动热压机的发展趋势是怎样的?
- 用户论文集 ▏化学吸附 ▏铱-铼共沉积乙醇处理后SiO2载体催化剂应用在甘油氢解反应
- 为什么近期单壁碳纳米角(CNH)的研究进展值得关注?
- 为什么介孔SiO2在药物递送领域的应用越来越多?
- FRITSCH飞驰球磨——不锈钢介导的水中球磨条件下定量H2生成实验研究
- 为什么MoS2在催化领域的研究进展值得关注?
- 飞纳台式扫描电镜助力纳米纤维在心血管组织再生中的研究
- 磷酸化修饰鬼臼果多糖的制备及生物活性
- DSR论文解读:Advanced Science News 报道中科院长春应化所新型非铂催化材料研究成果
- High-throughput preparation, scale up and solidification of andrographolide nanosuspension using hummer acoustic resonance technology(纳米混悬剂制备的前瞻性技术 - 蜂鸟声共振)
- 扫描电镜优秀论文赏析|飞纳台式扫描电镜电极材料上的应用
- 扫描电镜论文赏析-干旱影响杨树叶片及次生木质部发育的分子机制
- 压实度与密实度的区别
- 振实密度和压实密度的关系
- 勃姆石专用气流粉碎机分级机打散机
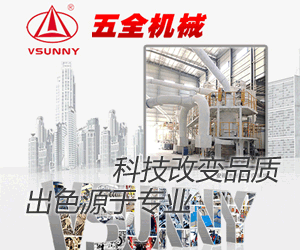