增加预破碎工艺 磨机的粉磨有效功率约1%,最高不超过9%,而破碎机的有效功率为30%左右,两者相差约10~30倍。采用“多破少磨”的工艺,即原有由磨内进行较粗物料的粉碎移到磨外由破碎机完成,这样可缓减磨机一仓负担,平均球径可适当下降,研磨功能增强,进入二仓的物料筛余下降,二仓负担减小,为二仓研磨体改用小钢段创造了条件,增强了研磨功能,保证了成品细度,颗粒级配合理且圆形度好,磨机台时产量提高约20%~30%,电耗下降(生料约5千瓦小时/吨,水泥约4千瓦小时/吨)。例如某厂原生料磨(Φ2.2×6.5m)入磨物料粒度25mm,平均为15mm,成品筛余为8%,台时产量25~28吨,电耗19千瓦时/吨,总装机容量530千瓦。在磨机前增设一台PSL70型喷射式破碎机、一台回转筛,入磨物料粒度降至5~7毫米,原有选粉机太小,制约磨机性能发挥,换成KX型高效高细转子式选粉机,总装机容量还稍小于530千瓦,生料成品筛余8%,台时产量为35~36吨,最高达38吨,电耗为14.7千瓦时/吨。每吨生料生产成本下降约2元,年节约近50万元。 长期以来,一般按入磨粒度小于25mm计算产量。如果加置预粉磨设备,如辊压机、立磨、筒辊磨或如冲击破、细颚破、细锤破、反击破等细碎机,降低入磨粒度,则能明显提高台时产量。根据实验、统计、归纳、换算,当入磨粒度从25mm降至2mm,增产幅度可达44%。值得注意的是,当入磨粒度降低,各仓的长度和研磨体的级配应作相应调整(适当减小粗磨仓的仓长,增加细磨仓的仓长),否则难以得到预期效果。 常用的预粉碎工艺主要有两种形式。其一是辊压机+球磨机粉磨工艺。水泥熟料在辊压机内受到强大的辊压力,从数十毫米被压碎至几个毫米甚至更细后再入球磨机。熟料颗粒经辊压粉碎的同时,内部也产生许多微裂纹,在球磨机内较容易进一步粉碎而很快进入粉磨阶段。在这种粉磨系统中,球磨机的主要任务只是粉磨,所以,粉磨仓可选用较小尺寸的研磨体,研磨体表面积的增大显然有利于粉磨效率的提高。采用这种工艺投资相对较大,技术要求高,但其设备及其配套技术已趋成熟,更适合于规模较大的立窑水泥厂的技术改造,必然会取得较好的经济效益。 辊压机在预粉磨系统中有两种应用方式:直流式、循环式。直流式的预粉磨系统,经辊压机挤压后的物料全部喂入筒式磨机内进行打碎粉磨,一次完成;循环式的预粉磨系统,经辊压机挤压后的物料,有最多不超过35%的一少部分返回,与新料一起重新喂入辊压机再次挤压。这样既可以改善辊压机的咬合情况,减少料饼中残存的大颗粒,保证喂入筒式磨机内的物料小颗粒比例增大,稳定操作,又可以提高粉磨效率,降低粉磨能耗。 筒式磨机可以采用开流操作,也可以采用圈流操作。筒式磨机可以是球磨机,也可以是管磨机,可根据具体要求确定。 这种预粉磨系统可将现有的筒式磨机产量提高20%~30%,单位成品电耗降低4~8kWh/t,即能耗低约12%~25%。采用循环式的预粉磨系统比直流式的产量提高幅度大,节能率高,但系统稍微复杂,所用设备也较多。具体采用哪种,应根据各厂实际情况确定。
1689

- 1KYKY钨灯丝扫描电镜-Version 2025.A.01
- 2KYKY场发射扫描电镜-Version 2025.A.01
- 3硅盐制样分析全自动研磨机AI海璐智能纳米粉碎机低温真超细磨粉机
- 4【样本】真空获得【2025年4月版】
- 5【样本】真空检漏【2024年9月版】
- 6【样本】真空应用【2023 7月版】
- 7畜牧行业杰曼称重料罐解决方案
- 8折叠屏、6G、新能源汽车,MIM/CIM工艺如何借势起飞?
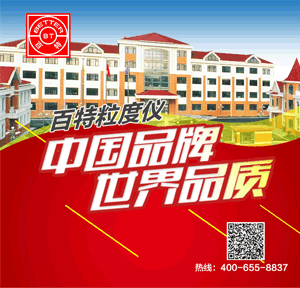
- TiZrHfNbMo 难熔高熵合金等离子体氢化及力学性能
- 《MSEA》重磅:增材制造7075铝合金,世界级难题有了新解法
- 为什么氮掺杂石墨烯的最新进展值得关注?
- 汽车一体化发光智能前脸设计难点
- 突破性进展!新型3D多孔碳银复合材料显著提升海水淡化效率
- Nature、Science接连报道石墨烯最新进展!
- 旋风分离除尘粉碎机售后维护与保养
- 为什么近期LDH的电催化应用频登顶刊?
- 苏州碳丰科技首席科学家程金生老师以本公司名义在国际上发表关于石墨烯纤维的论文《石墨烯纤维纳米复合材料的合成及氨基酸检测的分析应用》:
- 介可视·散装物料库存管理雷达全景扫描系统在料仓、堆场中的应用
- 磷酸化修饰鬼臼果多糖的制备及生物活性
- DSR论文解读:Advanced Science News 报道中科院长春应化所新型非铂催化材料研究成果
- High-throughput preparation, scale up and solidification of andrographolide nanosuspension using hummer acoustic resonance technology(纳米混悬剂制备的前瞻性技术 - 蜂鸟声共振)
- 扫描电镜优秀论文赏析|飞纳台式扫描电镜电极材料上的应用
- 扫描电镜论文赏析-干旱影响杨树叶片及次生木质部发育的分子机制
- 压实度与密实度的区别
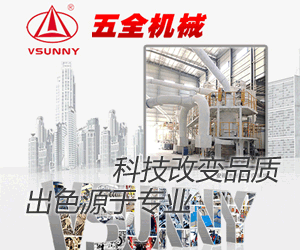