CMP浆体粒径分析:SPOS与费朗霍夫
半导体行业正在朝着更小的线宽和更多的层的方向发展。迈向这种高密度芯片技术的最重要的工艺考虑之一是对平面化步骤的更复杂的控制。抛光步骤受胶体分散金属氧化物浆料(CMP,化学机械平面化的简称)的影响,主要是二氧化硅和氧化铝,平均直径在10nm-200nm范围。这些浆料被用于放置晶圆片的旋转抛光垫上。在过去,激光衍射最常用来表征这些浆料的粒度分布。人们一直都知道,这些浆料中含有的体积百分比小于1微米的颗粒。这些颗粒会在晶圆片表面造成划伤和其他缺陷。本文将证明,由于测量的性质,激光衍射法不足以定量测定不合规格的浆料颗粒的浓度。另一方面,单粒子光学粒度(SPOS)可对颗粒进行计数,将被证明是表征CMP浆料的一个很好的工具。
高密度集成电路制造中最重要的工艺控制参数之一是抛光或平面化浆料的性能质量。在光刻或沉淀步骤后,这些浆料用于产生二维表面。在抛光过程中,CMP浆料是否诱发晶圆缺陷是非常重要的。人们早就知道,缺陷是由大的不合规格的粒子引起的。其中一些异常值主要是浆料颗粒的聚集物,而另一些则是在使用过程中引入的污染物。首先考虑聚集方面,我们必须认识到胶体系统在热力学上是不稳定的。此外,不当的混合或应用剪切所带来的化学变化也会加速浆料的最终分解。使问题更加复杂的是第二个方面,CMP浆料在使用之前和使用过程中都要经过大量的处理。例如,某些浆料由几个部分组成(化学部分和研磨部分),需要混合。硅浆通常以浓缩的形式出售,并在现场稀释。在这些准备过程中,可能会有污染物进入浆料中。此外,浆料通常储存在大容器中,抛光机从那里提取材料。在某些情况下,运输箱被存储在工厂其他地方,需要泵将浆料输送到很远的距离(30-50英尺)。泵送作用(剪切作用)可能使浆料聚集。浆料可以在距离上分离或离析将其带到抛光机,改变材料的性能特性。在任何情况下,在浆料制备过程中,直到使用的地方,都有足够的机会引入杂质,这可能会造成缺陷,以及各种环境,可能导致浆料变得不稳定和随着时间的推移聚集。因此,在平面化过程中的任何改进都需要对浆料抛光性能进行量化。最明显的方法应该是检测引起粒子的大缺陷的存在。在这个任务中,使用大量的颗粒大小测定技术似乎是明智的。一种常用的技术是激光衍射(LD)。激光衍射仪由于具有大的动态范围和快速的测量时间而得到广泛的应用。但是激光衍射装置有严重的局限性,这是它们所基于的原理所固有的。原因是激光衍射是一种集成技术,需要一个相对复杂的数学算法来获得粒径分布(PSD)的近似表示。从适当浓度的样品中获得的信号是散射/衍射强度与角度的图案。这种图案是有许多粒子同时被激光光源照射而产生的,他们各自的散射/衍射光在每个探测元件上混合在一起。产生的图案散射/衍射光线在每个探测器元件上混合在一起。由此产生的散射/衍射光强度与角度的关系不再像一个简单的最大值和最小值的交替。整个检测到的强度值(在时间上适当的平均)必须被一个适当的数学算法拟合,以便获得一个合理的准确和可重现的潜在PSD估值。
虽然激光衍射被认为是一种单一的方法,但事实上,它是基于费朗霍夫和米氏散射这两个理论的结合。前者依赖于由衍射现象明显引起的散射光强的图案。利用合适的探测器单元空间阵列,在相对于前向激光束方向的一个相对较小的角度范围内检测衍射光强度。理论上,在所有其他物理参数(如波长)固定的情况下,衍射光强度的最大值和最小值交替模式的角度范围与球形粒子的直径成反比。粒子越大,图案就越小。
然而,当颗粒直径小于约2微米时,由于衍射现象而产生的周期性强度变化的空间格局不再存在。相反,起作用的机制是光散射。因此,为了获得比这个费朗霍夫下限更小的粒子即使是中等可靠的尺寸信息,这几乎包括了典型CMPS的整个总体分布,必须实施基于米氏散射理论的第二次测量。该理论描述了由于单个粒子内不同点散射的单个光波的相互干扰而在较大角度下散射强度的变化。这种效应导致散射强度与角度有关,而散射强度与激光波长、粒子直径和粒子折射率有关。
此外,粒子吸收光的程度对散射强度随角度的变化也有显著影响。这个因素是由粒子折射率的阴影来解释的。因此,用户必须准备好提供浆料颗粒折射率的实分量和虚分量。最后,为了有效,光散射仪器必须成功的将费朗霍夫和米氏散射理论分析的结果结合起来,以便为PDS产生准备可靠的结果,这些结果既包括物理区域,也包括理论。对于基于这两种物理原理的仪器来说,要将两种完全不同的物理现象的结果正确的结合在一起,是一项困难的技术挑战,而且很大程度上,尚未解决。
当然,如果样品的PSD相对简单且表现良好,激光衍射可以相对有效地为CMP sully产生可靠的平均粒径。对于稳定的优质抛光液,通常满足这一标准。(尽管我们将在下面的例子中看到这种假设严重失败。)然而,在不稳定的情况下,PSD往往不再是精确可靠的分析,通过光散射方法。
相比之下,SPOS是一种基于光阻的单粒子计数器。通过计数粒子,SPOS可以提供无与伦比的分辨率和灵敏度的尺寸范围,大多数缺陷引起的粒子被发现(见应用说明156)。由于SPOS中的PSD是一次检测一个粒子,因此它基本上不会受到类似激光衍射中获得的PSD所表现出的不稳定和假象的影响。SPOS允许人们获得关于浆料颗粒区域的准确和可重复的定量信息。这是对浆料性能最重要的区域。让我们通过一些有代表性的数据来对比这两种技术。图1a包含了SPOS在两种氧化铈行浆料上得到的总体分析。众所周知,这些浆料在稳定性方面是有问题的,而且往往有大量的大颗粒。据观察,浆料1是一种性能良好的浆料,而浆料2被制造商指定为平均直径350nm。这些分布从1μm开始。正如预期的那样,PSD类似于平滑衰减的尾巴。浆料2的尾部明显比稳定浆料的尾部宽。1.这与浆料更倾向于沉淀有关。图1b包含了这些相同的体积加权分布。2.明显比更稳定的浆料的尾部更宽。这与更大的浆料倾向有关,他们更清楚地强调了两个样本之间的差异。
对于浆料2,大于2微米的颗粒贡献了相对较多的固体体积。此外,我们还可以从SPOS数据中计算出尾部粒子所贡献体积的绝对百分比。经测定,对于浆料1,大于1μm的颗粒占0.25%,而浆料2占0.68%。这个数据再次支持了浆体2明显聚集的观察结果。需要注意的是,虽然每个样品尾部的物理总量较小,但对比浆料性能的影响是显著的。
图2包含了在相同的两种氧化铈浆料上通过激光衍射得到的体积加权PSD。回想下,使用这种仪器的人必须输入实际折射率和虚折射率。一般来说,大多数材料的真实折射率是已知的,但虚折射率不是。图2a是实际折射率为1.65,需折射率为0.01i的计算结果,图2b是虚折射率为0.10i的计算结果。两组数据都是根据相同的散射光模式计算出来的。可以看出,在每次计算中,数据表明浆料2比浆料1的分布更广,颗粒更大,正如预期的那样。但这些数据仍然说明了从激光衍射中获得准确定量信息的困难。首先,虚折射率的选择使浆料1的平均直径发生了10%的偏移,大大改变了浆料2的分布形状,其次,浆料2的结果表明,固体体积的大部分(>70%)是由大于1μm的颗粒贡献的。这是不可能的,它与重量分析的结果以及SPOS的结果相冲突,后者确定了浆料中大于1μm的颗粒的固体百分比小于1%。这个数据证明了上面的观点,
下一个图包含的数据说明了激光衍射的另一个问题,它产生的伪影不能代表真正的颗粒大小。图3显示了超声处理后浆料1的体积加权PSD。回想一下,未超声样品的PSD(图2)由一个宽度相对较窄的单峰组成。在用浸入式声波探头进行20miao的声波处理后,平均值移得更高,第二个峰值出现在35μm处,其中包含50%固体体积。单独来看,这一数据表明声波作用导致浆料聚集。这与预期的行为相反。预计声波作用可以破坏弱结合的团聚体。
图4a包含看SPOS从同一样本得到的数字加权PSD。同样,只有尾巴被观察到,没有第二个峰在36μm的迹象被看到。比较大于1μm(0.23%)的颗粒在尾部的固体百分比,表明与未超声处理的样品没有变化(0.25%)。图4b为超声处理后浆料2的容积加权SPOS数据。它与图1中的未声波处理的数据叠加在一起。很明显,SPOS的结果在物理上更加真实。我们只能得出这样的结论:图3中的PSD是由散射光模式的反演产生的数学伪影造成的。这再次证明了使用激光衍射来预测浆料性能的危害。
作为进一步的粒子,考虑图5中的数据。这一数据是由硅基CMP获得的,它比铈氧化物浆料更常用。图5a包含了两种硅浆的SPOS尾数据(体积加权),从0.5微米开始。图5a包含了两种硅浆的SPOS尾数据(体积加权),从0.5微米开始。这些浆料的平均直径被认为在0.10至0.15微米范围内。可见,浆体A在2-20微米范围内的颗粒对体积的贡献显著,而浆体B没有大于5微米的颗粒。图5b包含了浆料a激光衍射得到的体积加权PSD(ID=1.08+0.10I),浆料B的PSD相同。可以看出,它由一个中心为0.15μm的单一对称峰组成,但没有大于1微米的粒子。这是一个合理的光散射结果,表明当样品PSD较窄时,激光衍射可以获得有用的平均直径信息。但是,另一方面,这个图再次说明了激光衍射灵敏度的缺乏。而SPOS可以看出这两种硅浆的差异,激光衍射则不能。
希望这些数据以及前面讨论的数据说明了量化大的差异粒子的重要性,当这些异常粒子出现在CMP浆料中时,可能会导致缺陷和芯片良率降低。在处理器价格下跌的时候,即使是少量的产量最大化也可以获得显著的经济回报。唯一能做到这点的技术是SPOS。
2463

- 1苏州天启高速混合机手册
- 2纳米石墨烯电镜检测
- 3纳米石墨粉粒度检测(复达)25-0630
- 4电池材料表征实践指南
- 5聚合物加工测试分析指南
- 6散量秤彩页
- 7无斗定量包装秤—毛重秤彩页
- 8电子舌在牙膏质量控制和研发的应用
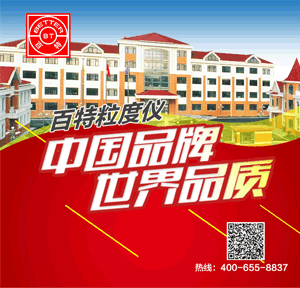
- 为什么AFM、NC等期刊频繁报道多孔水凝胶的最新研究进展?
- 蓝宝石的10大应用
- 《JMST》顶刊揭秘:激光3D打印高强铝合金的“强韧协同”奥秘——协同晶粒细化策略
- NC、AFM等期刊报道银纳米线最新研究进展!
- 为什么ZIF-67的最新研究进展值得关注?
- 经典介孔分子筛SBA-15又有新进展!
- 利用蜂鸟声共振技术对穿心莲内酯纳米混悬剂的开发、表征和分子动力学模拟
- 为什么核壳复合纳米材料的研究进展值得关注?
- Development, Characterization, and Molecular Dynamics Simulation of Andrographolide Nanosuspensions Utilizing Hummer Acoustic Resonance Technology
- 苏州碳丰科技首席科学家程金生老师以本公司名义在国际上发表关于石墨烯纤维的论文《石墨烯纤维纳米复合材料的合成及氨基酸检测的分析应用》:
- 介可视·散装物料库存管理雷达全景扫描系统在料仓、堆场中的应用
- 磷酸化修饰鬼臼果多糖的制备及生物活性
- DSR论文解读:Advanced Science News 报道中科院长春应化所新型非铂催化材料研究成果
- High-throughput preparation, scale up and solidification of andrographolide nanosuspension using hummer acoustic resonance technology(纳米混悬剂制备的前瞻性技术 - 蜂鸟声共振)
- 扫描电镜优秀论文赏析|飞纳台式扫描电镜电极材料上的应用
- 扫描电镜论文赏析-干旱影响杨树叶片及次生木质部发育的分子机制
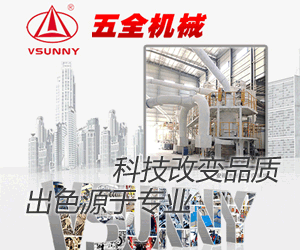